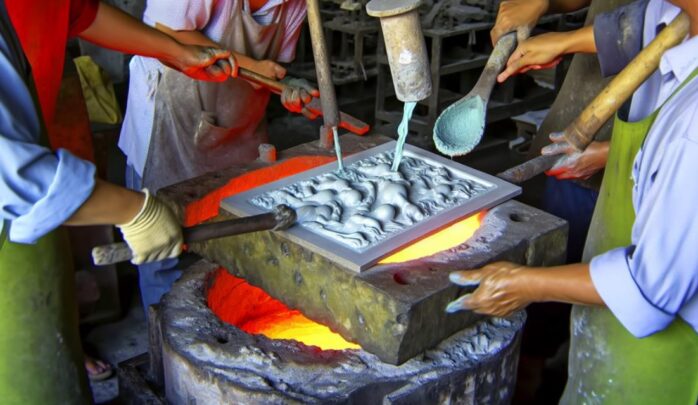
Are you fascinated by the art of metalworking? Do you find yourself drawn to the allure of transforming raw materials into magnificent creations?
If so, then prepare to embark on a journey of discovery as we unveil the technical know-how behind forging excellence in the realm of metalworking. From the rich history and evolution of this ancient craft to the essential tools and equipment required for success, we will delve deep into the world of metalworking.
Exploring fundamental techniques, specialized methods, and the art of achieving flawless metal finishes, we will unlock the secrets that will elevate your metalworking skills to new heights. Get ready to embark on this exciting adventure and watch as your creations come to life.
History and Evolution
Metalworking has undergone significant historical development and evolution, shaping various industries and contributing to the advancements of human civilization. The history of metalworking can be traced back thousands of years, with evidence of early metalworking techniques found in ancient civilizations such as Mesopotamia, Egypt, and China. Initially, metalworking focused on the extraction and shaping of metals such as copper, bronze, and iron. As societies progressed, metalworking techniques became more sophisticated, leading to the development of alloys, such as steel, and the invention of new tools and machinery.
The impact of metalworking on society can’t be overstated. The ability to work with metal revolutionized countless industries, from construction and transportation to medicine and communication. Metalworking techniques allowed for the creation of stronger and more durable structures, enabling the construction of taller buildings and more reliable infrastructure. Additionally, metalworking played a crucial role in the development of transportation, as it allowed for the construction of ships, trains, and automobiles. Metalworking also contributed to advancements in medicine, with the development of surgical instruments and prosthetics.
Essential Tools and Equipment
To effectively engage in metalworking, you must possess a range of essential tools and equipment. These tools not only enable you to shape and manipulate metal, but also ensure your safety and the longevity of your equipment.
Safety precautions should always be a top priority when working with metal. It’s crucial to wear protective gear such as safety goggles, gloves, and a face shield to shield yourself from sparks, flying debris, and harmful fumes. Additionally, proper ventilation is essential to prevent the buildup of toxic gases.
When it comes to equipment maintenance, regular care and attention are necessary to keep your tools in optimal working condition. Clean your tools after each use, removing any metal shavings or debris, and store them in a dry and secure location to prevent rusting. Sharpen your cutting tools regularly to maintain their effectiveness and ensure clean and precise cuts. Lubricate moving parts to reduce friction and prolong the lifespan of your equipment.
Fundamental Techniques and Processes
After ensuring you have the necessary tools and equipment for metalworking and taking the appropriate safety precautions, it’s essential to familiarize yourself with the fundamental techniques and processes involved in shaping and manipulating metal. Basic skills are crucial for any metalworker, and they serve as the foundation for more complex projects.
One of the most important basic skills in metalworking technical know how to measure and marking. Accurate measurements are essential for achieving precise cuts and bends. You must also learn how to use various hand tools effectively, such as files, hammers, and chisels. These tools allow you to shape and refine the metal to your desired specifications.
Safety measures should always be a top priority in metalworking. Before starting any project, make sure to wear appropriate protective gear, including safety glasses, gloves, and ear protection. It’s also important to secure the metal firmly to a workbench or vice to prevent accidents.
Additionally, understanding the different types of metal and their properties is crucial for successful metalworking. Different metals require different techniques and processes, so it’s important to research and learn about the specific metal you’re working with.
Specialized Metalworking Methods
One crucial aspect of metalworking involves employing specialized techniques and methods to shape and manipulate metal materials. These specialized metalworking methods are necessary for carrying out advanced applications and achieving intricate designs.
One such technique is known as forging, which involves the shaping of metal by applying localized compressive forces. There are various forging techniques used in metalworking, including open die forging, closed die forging, and press forging.
Open die forging is a process where the metal is deformed between two flat dies, allowing for greater flexibility in shaping. Closed die forging, on the other hand, involves the use of custom-shaped dies to create specific shapes and dimensions. Press forging utilizes hydraulic or mechanical presses to apply force and shape the metal.
These specialized forging techniques are extensively employed in advanced applications such as aerospace and automotive industries. For example, in the aerospace industry, forged components are used in aircraft engines and landing gear systems, where strength, durability, and precision are paramount. Similarly, in the automotive industry, forged parts are utilized in engine components and suspension systems, ensuring optimal performance and safety.
Mastering the Art of Metal Finishing
Mastering the art of metal finishing requires a deep understanding of various techniques and processes that are used to improve the appearance, durability, and functionality of metal surfaces. To achieve exceptional results, it’s essential to employ advanced polishing techniques and surface treatment methods.
Advanced polishing techniques play a crucial role in metal finishing. These techniques involve the use of abrasive materials and tools to refine the surface of the metal, removing imperfections and creating a smooth, reflective finish. Polishing can be done manually or with the aid of automated machinery. Different grades of abrasives are used depending on the desired level of smoothness and shine.
Surface treatment methods are equally important in metal finishing. These methods include processes like electroplating, anodizing, and powder coating, which enhance the properties of the metal surface. Electroplating involves depositing a layer of metal onto the surface through an electrochemical process, providing increased corrosion resistance and aesthetic appeal. Anodizing forms a protective oxide layer on the metal surface, improving durability and adding color options. Powder coating involves applying a thin, durable layer of powdered paint onto the metal surface, resulting in a vibrant and durable finish.
To truly master the art of metal finishing, one must explore and understand the intricacies of advanced polishing techniques and surface treatment methods. This knowledge, coupled with skill and experience, enables metalworkers to transform raw metal into exquisite, functional works of art.
Frequently Asked Questions
Are There Any Safety Precautions or Regulations That Need to Be Followed in Metalworking?
You must adhere to safety precautions and regulations in metalworking to avoid costly mistakes. Enhancing your metalworking proficiency requires understanding misconceptions and exploring alternative materials. Stay informed and protect yourself.
What Are Some Common Mistakes to Avoid When Starting Out in Metalworking?
When starting out in metalworking, it’s crucial to avoid common mistakes. Follow best practices to ensure success. Take precautions to prevent accidents and injuries. Pay attention to detail, use proper tools and techniques, and continuously improve your skills.
How Long Does It Typically Take to Become Proficient in This field?
It typically takes several years of dedicated practice and experience to become proficient in metalworking. During this time, you will need to learn and consistently apply safety measures and familiarize yourself with essential tools.
Are There Any Common Misconceptions or Myths About Metalworking?
Common misconceptions about metalworking abound, but let’s debunk them. One interesting statistic to emphasize this is that only 10% of people believe that metalworkers possess a high level of technical skill.
What Are Some Alternative Materials That Can Be Used in Metalworking Projects?
When working on metalworking projects, it is important to consider alternative materials that can be used. These materials offer unique properties and characteristics that can enhance the final product, expanding the possibilities in metalworking.